The ABC’s Of Air Compressor Terms
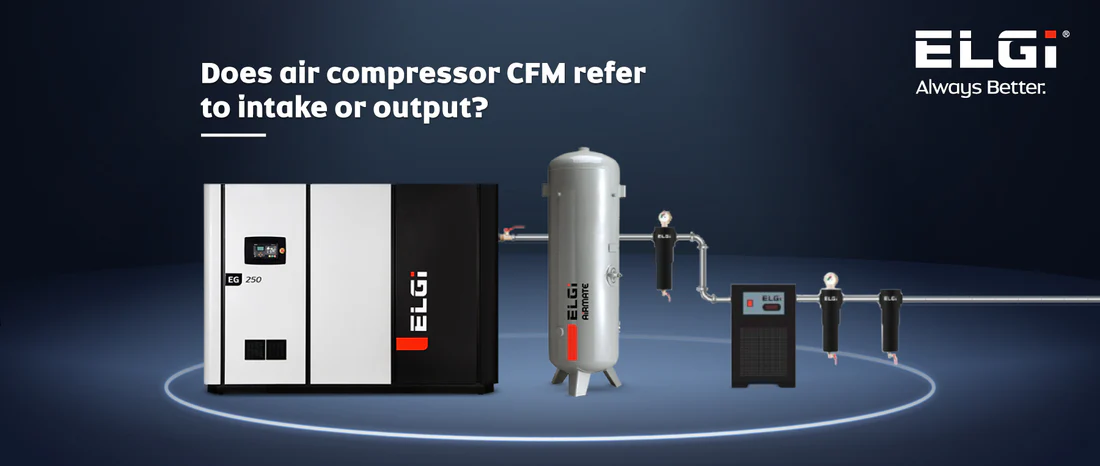
The ABC’s of Air Compressor Terms
Maximize the efficiency of and fully understand your air compressor system. Here are industry key terms to understand in regards to air compressor parts, systems, and more.
Air Compressor Systems and Processes
- Aftercooling: The removal of heat when the compression process is complete. An aftercooler is a mechanical heat exchanger designed to remove the heat-of-compression from a compressed air stream and to condition the air so it can be used in air-operated equipment.
- Full-Load: The operation of an air compressor at full speed, having a completely open inlet and discharge delivering upper limit airflow. Some air compressors are not designed to run continuously at full load because they will overheat, such as reciprocating air compressors. On the other hand, screw air compressors are designed to run at full load and will produce much cooler and cleaner air, which can then be sent directly to an air dryer to remove water vapor.
- Load/Unload Control: A method of control that permits the compressor to run either at no load or at complete load at the same time that the driver remains at a constant speed. Load/unload control is an attempt to match air delivery to the demand. It is also called constant speed control.
- No Load: When an air compressor is running at full RPM and is wide open, but no air is sent because the inlet is either closed off or modified and will not allow inlet air to be trapped.
- Sole Plate: The pad the compressor is mounted on when it requires a stable foundation to anchor the motor. This is implanted in concrete and usually metallic surfaces.
Air Compressor Parts
- Air Pressure Regulator: A component of an air compressor that allows the user to adjust the air pressure in the air line. This is a vital function because many pneumatic cylinders would be harmed by overly powerful air.
- Casing: The element that houses the rotor and other related internal components of an air compressor. This includes the integral inlet and discharge connection. In an engine with an axial-flow compressor, the stator vanes are mounted in the compressor casing.
- Cylinder: The piston compartment in an actuator or reciprocating compressor. At the top of the cylinder, you’ll find a valve head that holds the inlet and discharge valves. Typical compressors come in 1 or 2-cylinder versions to suit the requirements of the tools they power. Most of the 2-cylinder models operate just like single-cylinder versions, except that there are two strokes per revolution instead of one.
- Discharge Piping: The piping that delivers compressed air to the filters, dryers, receiver tanks, and distribution headers contaminant-free and with little or no pressure-loss. The pipes must be able to withstand the discharge air’s high temperatures that can range from 250 to 350 degrees Fahrenheit (for centrifugal, oil-free rotary screw, and reciprocating types) or from 200 to 220 degrees Fahrenheit (for lubricant-cooled rotary screw compressors). Stainless steel or coated aluminum are the top choices recommended for interconnecting piping materials that lead from the compressor to the filters and dryers when the compressed air is oil free. It will resist corrosion better than standard schedule 40 black iron.
- Drive: A flange-mounted belt drive, motor or direct coupling between the engine or motor and the compressor.
- Impeller: The component of the rotating element of a dynamic compressor that gives energy to the flowing medium through centrifugal force. An impeller is comprised of blades that rotate with the shaft. It transfers energy from the motor that drives the pump to the fluid being pumped. These are found in centrifugal and axial air compressors. Air is drawn into the center of a rotating impeller with radial blades and is pushed toward the center by centrifugal force. This radial movement of air results in a pressure rise and the generation of kinetic energy. In an axial compressor, the air flows parallel to the axis of rotation, while the flow through a centrifugal compressor is turned perpendicular to the axis.
- Intake Check Valve: The valve intended to stop air pressure and volume from slipping out of the compressor tank back into compressor heads when the compressor is not running. The valve is operated pneumatically. Air is applied to a control port pressurizing a piston. Then, the piston opens or closes the valve, and a spring returns the valve to its starting position. The intake valves are designed with an independent poppet so that back flow is prevented. The intake can be designed as normally open or normally closed. A normally open valve would have to be modulated closed for the system. A typical use is to control the airflow into a rotary screw compressor. The valve would be modulated open or closed by the compressor control system to meet downstream air demands.
- Intercooler: Heat exchangers that eliminate heat produced during compression between the stages of a compression system. The lower density of cool air makes it easier to compress than hot air. Ideally, the air should be as close to the ambient air temperature as possible. Typically, the intercooler is able to cool the compressed air within 20-30 degrees of the ambient air temperature. The cooling process begins by passing cool water into the intercooler and manifold through tubes. Fins attached to the tubes add stability and aid in increasing the cooling surface area. Moisture from the lower velocity air condensates and separates from the air as it passes through the intercooler. The moisture drains from the compressor through a valve located at the bottom of the intercooler enclosure. This method of removal prevents loss of valuable compressed air, increasing the overall efficiency of the compressor by not having to compress the entrained water remove during the intercooling process.
- Pressure Inlet: The total pressure (static plus velocity) at the inlet flange of the compressor.
- Rotor: A revolving element of a compressor. It consists of the impeller and shaft and may have shaft sleeves and a thrust balancing device. In the rotary screw element of the screw air compressor, the rotors have different kinds of bearings on both sides, so they run smoothly for years without any maintenance. There are usually two pairs of bearings on both sides: bearings for radial loads (loads because of the turning of the rotors) and axial bearings. (explain axial bearings)
- Shaft: The part that the rotating elements are attached to and through which energy is transferred from the prime mover.
Air Compressor Pressure and Ratios
- Backflow: A condition caused by a difference in pressure in which air will flow back into the distribution pipes rather than in the intended direction.
- Collapse Pressure: The lowest amount of differential pressure something is able to withstand without deformation.
- Compression/Pressure Ratio: The ratio of the absolute inlet pressure to the absolute outlet pressure. It typically applies to a single stage of compression but could also apply to a full multistage compressor.
- Load Factor: The ratio of the maximum rated compressor load to the average compressor load within a certain period.
- Maximum Pressure Rating: The highest pressure level recommended for a compressor.
- Pressure Inlet: The total pressure (static plus velocity) at the inlet flange of the compressor.
- Pressure Rise: The difference between the intake pressure and the discharge pressure.
Contact our sales team for more questions! sales@penryair.com or (877) 388-4111